In the world of model railroading, technological advancements are pushing the boundaries of realism and interactivity. Gone are the days when model trains simply moved along fixed tracks with manual control. Today, hobbyists and professionals alike are integrating cutting-edge automation and control systems to bring their miniature worlds to life. One of the most critical components driving this revolution is the USB I/O controller, which serves as the backbone for connecting various devices and automating processes. With the addition of tools like the Mach 4 motion controller and slip ring testing systems, model railways are becoming more sophisticated and dynamic than ever before.
This article will explore how the USB I/O controller plays a pivotal role in model railway automation, examine the significance of slip ring tests for smooth operation, and highlight the integration of Mach 4 motion controllers to enhance performance and control. We’ll also dive into practical scenarios where these technologies intersect, providing readers with a comprehensive understanding of their functionality and importance in modern model railroading. Whether you’re an enthusiast looking to upgrade your setup or a professional working with high-tech railway systems, this article will provide valuable insights into the tools and technologies that are shaping the future of model railway automation.
Understanding the PoKeys57U USB I/O Controller and Its Role in Model Railway Automation
When it comes to building a modern, automated model railway system, one of the most essential components is a reliable controller that bridges the physical world of model trains and their complex automated software environment. The PoKeys57U USB I/O controller is a versatile and powerful tool that allows model railway enthusiasts to control, monitor, and automate every aspect of their layout, from track switching to managing signals and controlling automated scenery. It provides a high level of integration and flexibility, making it a critical piece of hardware in the model railway automation ecosystem.
In this chapter, we will explore the PoKeys57U, its features, its role in model railway automation, and how it can be used to achieve seamless, synchronized control of your model railway. By understanding how this USB I/O controller works, hobbyists can leverage its full potential to create an automated railway that operates with the precision and realism of a real-world rail system.
What is the PoKeys57U USB I/O Controller?
The PoKeys57U is a multifunction USB interface controller designed to manage a wide range of tasks in automation systems. As an I/O (input/output) controller, it can handle digital and analog signals, providing a bridge between the computer software and the physical hardware of a model railway layout. This small yet powerful device can control various components such as track switches, sensors, lights, motors, and more, making it an ideal choice for automating model railroads.
One of the standout features of the PoKeys57U is its ability to interface with a variety of different input and output devices. It has a substantial number of digital and analog inputs and outputs, making it suitable for both simple and highly complex model railway systems. With its USB connectivity, it can easily be linked to a computer running automation software, enabling hobbyists to control their layouts directly from their PC. This allows for advanced scheduling, real-time feedback, and intricate control of multiple trains and other moving parts, like signals, gates, and automated scenery.
In a model railway system, the PoKeys57U acts as the central hub, ensuring that all components of the layout can be connected, monitored, and controlled from a single point. Its compatibility with other systems, including motion controllers, sensors, and even systems like Mach 4, means that it plays a crucial role in creating an integrated, fully automated environment.
How the PoKeys57U Enhances Model Railway Automation
In the context of model railway automation, the PoKeys57U provides hobbyists with a powerful tool to manage all aspects of their layout’s operation. From controlling track switches and signals to regulating train movements and lighting, this USB I/O controller offers unparalleled flexibility and control.
One of the primary uses of the PoKeys57U is to control track switches and signals. On a typical model railway, managing the movement of trains requires not only controlling their speed and direction but also ensuring they stay on the correct tracks. The PoKeys57U can interface with track switch motors, allowing operators to change tracks automatically based on pre-programmed schedules, sensor feedback, or even real-time interactions. This is especially useful when integrating with advanced software systems that can coordinate multiple trains running on the same layout.
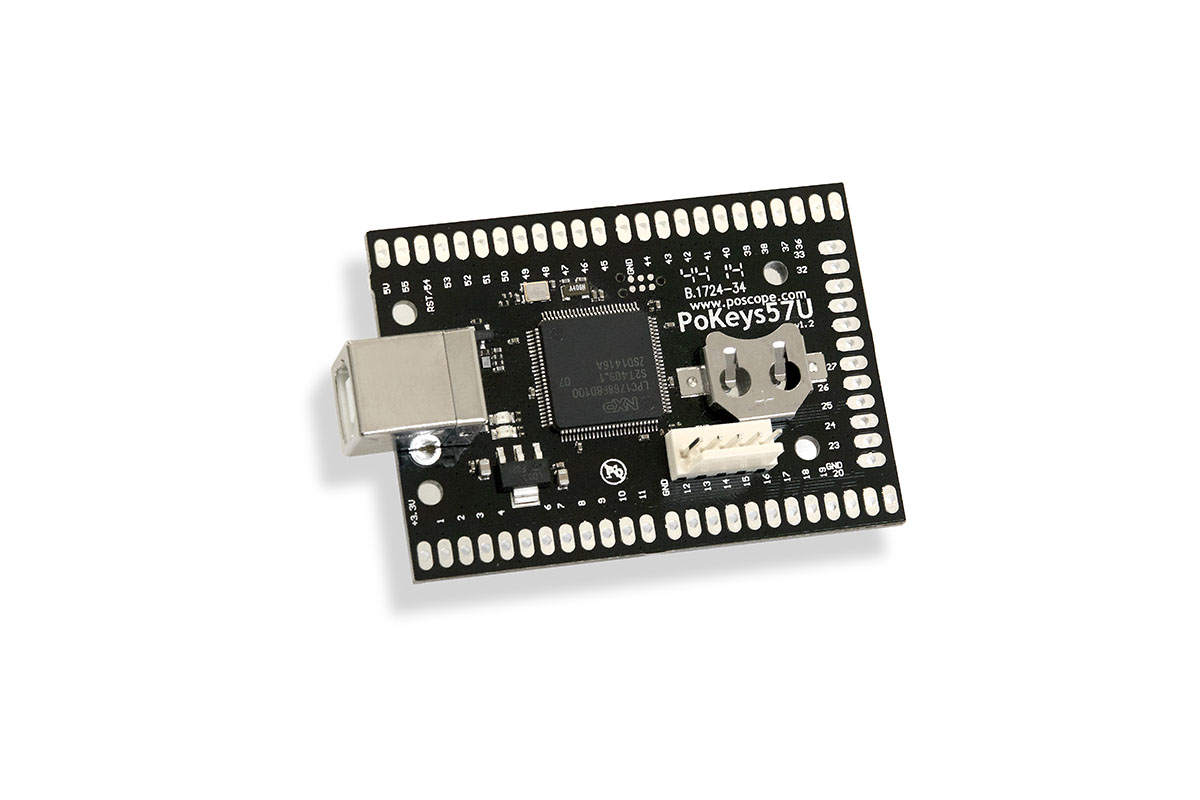
The PoKeys57U also excels in controlling the lighting systems on a model railway. By interfacing with digital and analog outputs, it can manage the operation of station lights, street lamps, and even automated scenery lighting. For example, operators can program lights to turn on or off based on specific events, such as when a train passes a station or a signal changes state. This ability to automate lighting adds another layer of realism to model railways, making them more dynamic and immersive.
Additionally, the PoKeys57U can be used to monitor sensors that detect the position and speed of trains, ensuring that the system remains responsive to changes in real-time. For example, sensors placed along the track can provide feedback to the controller, allowing it to adjust train speeds, switch tracks, or trigger events such as the opening of crossing gates when a train approaches. This level of feedback ensures that the layout runs smoothly, with minimal human intervention, while maintaining precise control over all moving elements.
Integration with Other Systems: PoKeys57U and Motion Controllers
One of the key advantages of the PoKeys57U is its ability to integrate seamlessly with other automation systems. A perfect example is its integration with motion controllers like the Mach 4 system. While the PoKeys57U handles the I/O and control of track switches, sensors, and lighting, the Mach 4 motion controller can be used to control the actual motion of the trains and other moving parts.
Together, these systems provide a comprehensive solution for model railway automation. The PoKeys57U can handle all of the necessary input and output signals, while the Mach 4 motion controller ensures that train movements are smooth, synchronized, and lifelike. The combination of these two technologies allows for real-time control and monitoring of all aspects of the railway, from train speed to track switching and automated actions triggered by sensors.
For example, a train might be programmed to automatically slow down when approaching a station, with the PoKeys57U monitoring the track sensors to determine the train’s position. The Mach 4 controller then takes over, adjusting the speed and ensuring that the train stops at the station with perfect timing. This level of integration creates a seamless and realistic railway experience that would be difficult to achieve with manual control alone.
Benefits of Using the PoKeys57U in Model Railway Automation
There are several benefits to incorporating the PoKeys57U USB I/O controller into a model railway system. First and foremost, it simplifies the process of automating a model railway layout. Rather than using a multitude of separate controllers for different components, the PoKeys57U provides a centralized interface that can manage all I/O tasks in one place. This reduces clutter and streamlines the automation process, making it easier for operators to focus on the creative and operational aspects of their layout.
The PoKeys57U is also highly flexible, allowing for a range of custom configurations to suit different types of layouts. Whether you have a small, basic railway or a large, complex system with multiple tracks, stations, and automated scenery, the PoKeys57U can be adapted to meet your needs. Its wide range of inputs and outputs makes it suitable for everything from controlling individual trains to managing intricate switching and signaling systems.
Another significant benefit of the PoKeys57U is its ease of integration with existing systems. Many model railway enthusiasts already use motion controllers, sensors, and automation software, and the PoKeys57U is designed to work seamlessly with these components. Whether you’re using a Mach 4 motion controller, a slip ring system for continuous power to rotating components, or advanced sensor feedback for train tracking, the PoKeys57U can tie it all together in a cohesive, efficient system.
Challenges and Considerations
While the PoKeys57U offers a range of powerful features, it’s important to understand that setting up and configuring the controller can take some time, especially for those new to model railway automation. The controller requires a certain level of technical knowledge to integrate with other systems, program inputs and outputs, and fine-tune the performance of various components. However, once the system is set up, it provides an incredibly reliable and flexible solution for managing the complexity of automated model railways.
Additionally, while the PoKeys57U is a versatile tool, it may require additional components such as motor drivers, sensors, or relay boards to fully integrate with specific parts of your layout. Depending on the scale and complexity of your railway, you may need to invest in additional equipment to make the most of the controller’s capabilities.
The PoKeys57U USB I/O controller is an indispensable tool for model railway automation, providing enthusiasts with a powerful and flexible system for controlling all aspects of their layouts. By offering seamless integration with motion controllers like Mach 4, as well as the ability to manage sensors, switches, lighting, and more, the PoKeys57U serves as the backbone of a fully automated, realistic model railway system. Its versatility, ease of integration, and comprehensive I/O capabilities make it an ideal choice for both beginners and advanced model railway hobbyists looking to take their layouts to the next level. Whether you’re controlling a small setup or an expansive railway system, the PoKeys57U helps ensure that every component operates in perfect harmony, bringing your model railway to life with precision and ease.
Read also:
- A Comprehensive Guide to DAQ Devices, Raspberry Pi Temperature Loggers, RC Simulator Interfaces, and Ethernet I/O Controllers
- Bridging Technology and Creativity: The Synergy of USB I/O Controllers, DIY Orchidariums, Flat Cable Cutters, and Flight Simulator Interfaces
Model Railway Automation: From Concept to Reality
Model railway automation has evolved dramatically over the past few decades. What once required manual control of every signal, train, and track switch can now be achieved with advanced automation systems that bring a level of realism and efficiency previously unimaginable. At the core of this transformation is the ability to integrate various technologies that work together seamlessly, ensuring smooth operation and enhancing the experience of both operators and viewers.
In this chapter, we will explore the concept of model railway automation, the technologies involved, and how they work together to create a fully automated railway system. We will examine the benefits of automation, the role of the USB I/O controller, and how automation systems can be designed to mimic real-world operations. By understanding the principles and technologies behind model railway automation, hobbyists and enthusiasts can begin to take full advantage of these innovations in their own layouts.
The Basics of Model Railway Automation
At its core, model railway automation involves the use of electronic systems to control various aspects of a model railroad, including train movements, signaling, track switching, and environmental effects such as lighting and sound. Automation allows for the creation of intricate, dynamic layouts that require minimal human intervention, offering an immersive experience that simulates real-world rail operations.
The first step in automating a model railway is understanding the components that need to be controlled. These typically include the trains themselves, track switches (or points), signals, and the layout’s various sensors. A modern automated model railway setup might also include features such as crossing gates, station stops, automated lighting, and sound effects. These components must all be interconnected to allow for smooth operation and synchronized control.
The most critical component in modern model railway automation is the central controller, which coordinates all the system’s activities. USB I/O controllers play a vital role in this system, as they act as the interface between the physical components of the railway and the software that controls them. These controllers manage input and output signals from devices like sensors, switches, and trains, and allow the system to respond to real-time conditions on the tracks.
How Automation Enhances Realism
One of the most significant advantages of automation is the ability to create highly realistic scenarios on the model railway. In a fully automated system, trains don’t simply run along preset routes; instead, they respond to track sensors and switches in a way that mimics real-world operations. For example, the system can be programmed to stop trains at stations, change tracks at junctions, and control the speed and direction of locomotives based on real-time feedback.
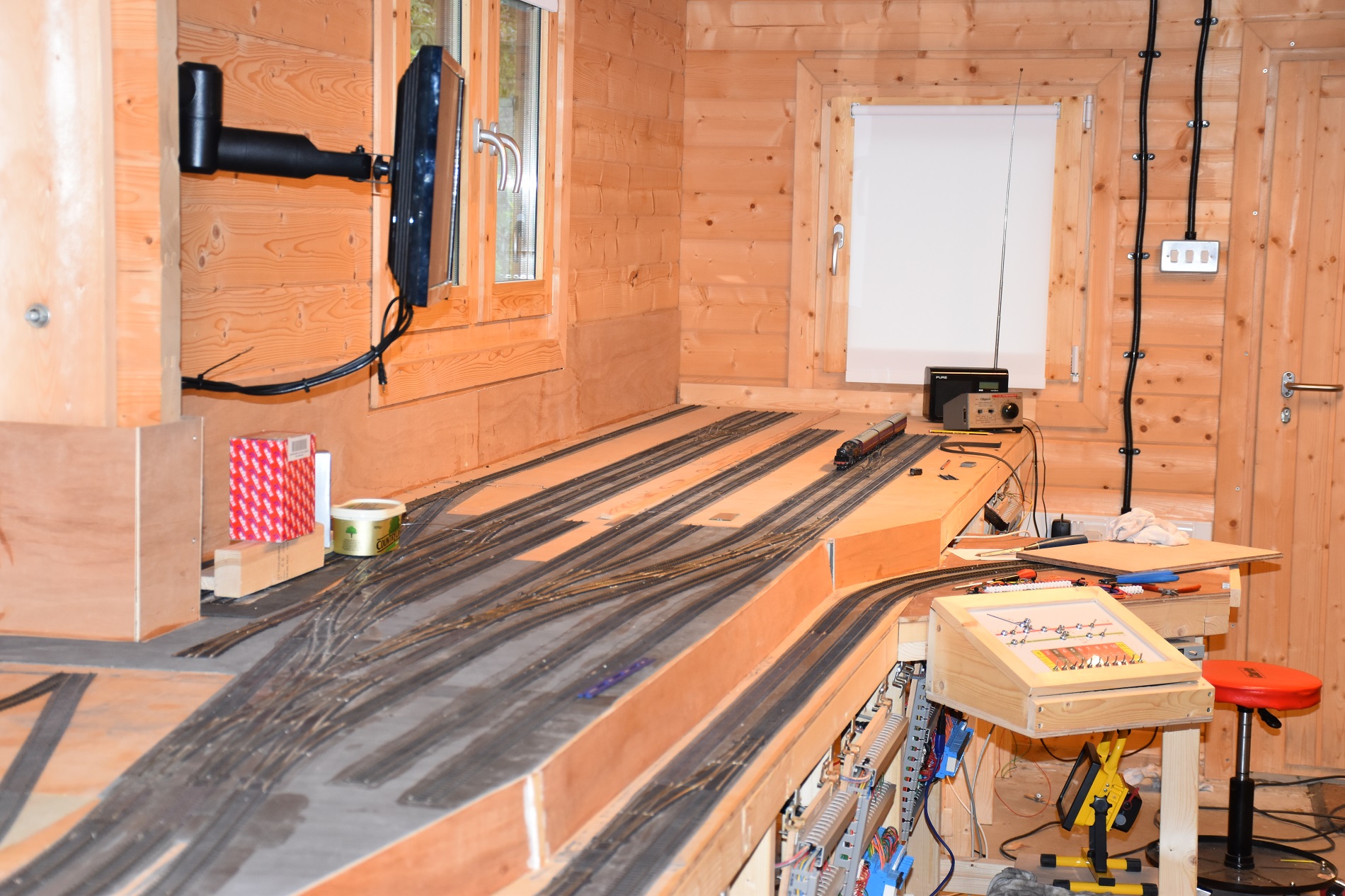
Using advanced automation software, model railway enthusiasts can design complex operating schedules that simulate real-world train services. This could include timed departures from stations, freight handling, and even automated station announcements. Trains can be programmed to operate in a manner similar to actual railroads, where multiple trains run concurrently, and signals are used to ensure safe spacing between them. The inclusion of real-time sensor data, such as track occupancy sensors, ensures that the system responds dynamically to changing conditions, further enhancing the authenticity of the operation.
For example, if a sensor detects that a train has entered a block, the system can automatically switch signals to ensure that no other train enters that section of track, preventing collisions. Similarly, track switches can be set to automatically change when a train approaches, ensuring smooth transitions between tracks and eliminating the need for manual intervention.
The Role of the USB I/O Controller in Automation
As we mentioned in the previous chapter, the USB I/O controller is a crucial part of the automation process, serving as the bridge between the physical devices on the model railway and the digital control software. Through this controller, signals are sent to and received from various input/output devices, such as sensors, motors, and switches.
The USB I/O controller enables the creation of a two-way communication channel between the computer and the railway system. For instance, it allows sensors placed on the track to communicate with the computer, informing it of the train’s position. This data is then used by the software to control signals, switches, and the train’s movements. In turn, the software sends commands to the USB I/O controller to adjust the layout’s components accordingly.
The versatility of the USB I/O controller allows for the integration of a wide range of devices, from simple switches to more complex feedback systems. This flexibility makes it an ideal solution for automating even the most complex model railway layouts. Whether it’s controlling a single train on a small oval track or managing multiple trains on an intricate network of tracks, the USB I/O controller ensures that everything runs smoothly and efficiently.
Moreover, USB I/O controllers are designed to be scalable, meaning they can be used for both small and large model railway systems. As the layout grows and more devices are added, additional I/O controllers can be connected to the system, expanding the control and automation capabilities without the need for an entirely new setup.
The Benefits of Full Automation
Model railway automation offers a wide range of benefits, from improved operational efficiency to enhanced realism. By automating key processes, model railroaders can focus more on the creative aspects of their layouts, such as designing scenery, building intricate structures, and fine-tuning the aesthetic elements. Automation takes care of the repetitive and time-consuming tasks of managing train movements, track switches, and signals, allowing operators to step back and enjoy the intricacies of their creations.
Another significant advantage of automation is safety. In manual model railroads, human error can lead to collisions, derailments, or other accidents, especially when multiple trains are running simultaneously. With automated systems, these risks are minimized, as the system can detect potential issues in real time and make adjustments accordingly. For instance, if a train is about to collide with another, the system can automatically stop one train or change its direction to avoid an accident.
Moreover, automation increases the potential for a more interactive experience. In larger layouts, where multiple trains are running on different tracks, it can be challenging for a single operator to manage everything manually. Automation enables the creation of more dynamic and complex operations, with trains running independently yet still coordinated to create a sense of realism. By programming the system to handle tasks such as station stops, freight operations, and signal changes, operators can enjoy a more immersive experience that feels much closer to real-life railway operations.
Challenges in Implementing Automation
Despite the many benefits, model railway automation does present some challenges. One of the most significant hurdles is the complexity of designing and implementing an automated system. It requires not only a basic understanding of model railroading but also a good grasp of the electronics, sensors, and software involved. The initial setup of automation systems can be time-consuming, requiring careful planning and configuration of all components to ensure they work together properly.
Another challenge is the need for troubleshooting. As with any complex system, issues can arise, from faulty sensors to software glitches. This means that model railway enthusiasts must be prepared to diagnose and resolve technical problems, which may require advanced knowledge of both hardware and software.
Finally, the cost of automation can be a barrier for some hobbyists. While USB I/O controllers provide a cost-effective solution, the cost of other components—such as sensors, feedback systems, and automation software—can add up quickly, especially for larger layouts.
Model railway automation offers a wealth of possibilities for enthusiasts seeking to elevate their layouts beyond simple, manual operation. By integrating advanced technologies such as USB I/O controllers, model railroads can achieve a new level of realism, interactivity, and efficiency. Automation allows for precise control over train movements, track switching, and signaling, resulting in a dynamic, lifelike experience that mimics real-world rail operations. While there are challenges in setting up and maintaining automated systems, the benefits they provide make them an invaluable tool for modern model railroaders. Whether for personal enjoyment or as part of a professional-grade layout, automation is transforming the world of model railroading and pushing the boundaries of what’s possible.
The Importance of Slip Ring Testing in Model Railway Systems
In the pursuit of realistic and smooth-running model railways, every component must function flawlessly to ensure seamless operations. One often overlooked, but critical element in complex railway setups is the slip ring. Slip rings are used in various rotating mechanical systems, including those found in model railways, to allow continuous electrical connections between stationary and moving parts. In this chapter, we will discuss the role of slip rings in model railway systems, the need for slip ring testing, and how this testing helps maintain high performance and prevent operational failures.
What is a Slip Ring and Why is It Important?
A slip ring is an electrical component used to transmit power or signals to a rotating object without the need for physical wires to twist or break. In model railways, slip rings are typically found in systems where trains need to receive power from stationary tracks while maintaining motion, such as in motorized locomotives or turntables. They are also used in other rotating elements of a model railway layout, such as automated cranes or rotating scenery pieces.
Slip rings allow these rotating parts to maintain a continuous flow of electricity or data signals, ensuring that electrical power, control signals, and sensor data can be transmitted without interruption, even as the components rotate or move. For example, on a motorized turntable, the slip ring allows the stationary electrical system to supply power to the rotating deck, while enabling the rotation to take place without tangling or losing connection.
For model railroads, ensuring that the slip ring system operates smoothly is essential. If the slip ring fails or doesn’t perform optimally, it can result in electrical failure, loss of signal transmission, or poor performance of rotating elements, such as malfunctioning locomotives or faulty automated systems. This is where regular slip ring testing becomes crucial.
The Role of Slip Ring Testing in Model Railway Automation
Slip ring testing is an essential part of maintaining and optimizing model railway systems. Over time, slip rings can wear down due to friction or environmental factors, leading to issues like signal degradation, electrical shorts, or power loss. Routine testing helps to identify these potential problems before they result in operational disruptions.
The main goal of slip ring testing is to ensure that the electrical connection between rotating and stationary parts remains stable and efficient. This is particularly important in automated systems where precision and reliability are key. When using automation systems like the USB I/O controllers discussed in earlier chapters, slip rings must provide consistent power to sensors, switches, and other moving elements. If a slip ring fails, even briefly, it could cause signals to drop out or mechanical elements to stop functioning, disrupting the entire system.
There are a variety of testing methods that can be used to assess the performance of slip rings. These tests typically involve checking for electrical continuity, measuring the resistance of the connection, and verifying that there is no excessive wear or damage to the components. Additionally, slip ring tests can help ensure that there is no signal interference or noise in the system, which could affect the performance of sensitive equipment such as motion controllers or sensors. Regular testing and maintenance allow for the early detection of these issues, minimizing downtime and ensuring that the system remains in optimal working condition.
How Slip Ring Testing Works
Slip ring testing generally involves using specialized equipment to monitor the electrical performance of the slip ring assembly. Testing can be done manually or using automated diagnostic tools, depending on the complexity of the layout and the systems in use. In a typical manual test, an operator will rotate the slip ring by hand or by activating the corresponding motor to check for any irregularities in electrical continuity. This can help identify areas where the connection might be weak, or where friction has caused the electrical connection to degrade.
A more advanced method of testing involves using diagnostic tools that can measure the performance of the slip ring in real-time. These tools are designed to detect issues such as voltage drops, resistance imbalances, or signal noise. By continuously monitoring the slip ring’s performance, these systems can alert the operator to potential problems before they cause a malfunction. In larger or more complex railway systems, automated testing can be set up to run periodically, ensuring that the slip rings are always functioning at peak efficiency.
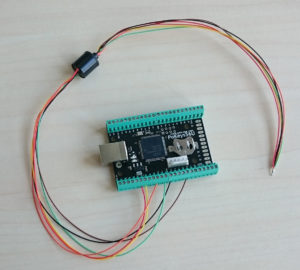
In some cases, visual inspection may also be performed to assess the physical condition of the slip rings. This can include checking for wear on the brushes that maintain contact with the rotating surface of the slip ring, as well as looking for any signs of oxidation or debris buildup, which can affect the quality of the electrical connection.
The Consequences of Neglecting Slip Ring Testing
Neglecting slip ring testing can have significant consequences for model railway operations. One of the most immediate risks is the failure of power transmission. If a slip ring begins to malfunction or loses its connection, it can cause power loss to key components such as motors, lighting, or track sensors. In automated model railways, where precise control is needed for the seamless operation of multiple trains or other moving elements, even a short disruption can throw the entire system off balance.
For example, if a slip ring fails in a system that uses motion controllers like the Mach 4, it could result in erratic or unpredictable train movements, causing delays, collisions, or system errors. Similarly, a faulty slip ring could lead to signal failures, causing automatic track switches to malfunction or preventing the system from accurately detecting the position of trains. In extreme cases, a slip ring failure could result in equipment damage or the need for expensive repairs.
Beyond technical issues, neglecting slip ring testing can also lead to frustration for model railroad operators. Automated systems that are designed to run smoothly and independently can be severely compromised if slip rings are not functioning properly. A model railway setup that suddenly fails to perform as expected can take away from the enjoyment and satisfaction that comes with operating an automated railway system.
The Benefits of Regular Slip Ring Testing
Regular slip ring testing ensures that the critical components of a model railway system remain in good working order, preventing costly downtime and system failures. By identifying potential problems early, hobbyists can make necessary adjustments, repairs, or replacements before issues escalate. This helps to maintain the performance and reliability of the system, allowing for a more enjoyable and hassle-free model railway experience.
In addition to preventing failures, slip ring testing also contributes to the overall longevity of the equipment. By addressing issues such as wear, corrosion, or debris buildup early on, operators can extend the life of their slip rings and avoid the need for frequent replacements. This not only saves money but also minimizes the impact of maintenance on the operation of the model railway.
In model railway systems, where precision, reliability, and smooth performance are critical, slip rings play a vital role in ensuring continuous power and signal transmission. Regular slip ring testing is essential to prevent potential failures, maintain system performance, and ensure the longevity of the equipment. By performing routine checks, hobbyists can keep their automated railway systems running smoothly and enjoy a seamless and immersive experience. With technologies like the USB I/O controller, Mach 4 motion controllers, and other automated systems, slip rings help create the intricate, dynamic environments that are the hallmark of modern model railroads. By taking the time to test and maintain these components, operators can ensure that their layouts continue to run efficiently, delivering both operational reliability and enjoyment for years to come.
The Role of Mach 4 Motion Controllers in Model Railway Automation
In the world of model railway automation, precision and smooth motion are paramount. Achieving this level of control requires specialized equipment designed to manage not only the operation of trains but also the intricate movements of other elements like turntables, signals, and automated scenery. This is where the Mach 4 motion controller comes into play. As one of the most advanced motion control systems available, Mach 4 offers a range of capabilities that can elevate any model railway setup, whether it’s for a small, home-based layout or a large-scale professional project.
In this chapter, we will explore the role of the Mach 4 motion controller in model railway automation. We will look at its capabilities, how it integrates with other components such as USB I/O controllers and slip rings, and why it is an essential tool for achieving precise, lifelike motion control in modern model railroads.
What is the Mach 4 Motion Controller?
The Mach 4 motion controller is a high-performance software-based control system designed for precise motion control in various applications, including CNC machines, robotics, and automation systems like model railways. It works by sending commands to stepper motors, servo motors, and other actuators to control their movements with exceptional accuracy. Mach 4 is known for its flexibility, user-friendly interface, and wide compatibility with various hardware and software, making it ideal for managing the complex movements of trains and other moving parts in a model railway.
In model railway automation, the Mach 4 motion controller can be used to control everything from the movement of locomotives on the tracks to the rotation of turntables, the adjustment of signals, and even the operation of automated scenery elements such as bridges or cranes. By integrating Mach 4 with the USB I/O controller and slip ring systems discussed in previous chapters, hobbyists can create a fully synchronized and highly detailed railway system with precise control over every moving element.
How Mach 4 Motion Controllers Drive Automation
The primary function of the Mach 4 motion controller in model railway systems is to ensure the smooth, precise movement of trains and other rotating components. When integrated with the USB I/O controller, Mach 4 allows the software to send commands to various actuators based on sensor input, real-time conditions, or pre-programmed schedules.
One of the key features of Mach 4 is its ability to handle multiple motion control tasks simultaneously. This is particularly useful in large or complex model railway layouts, where multiple trains or moving elements need to be controlled in tandem. For instance, Mach 4 can simultaneously manage the movement of trains on separate tracks while coordinating the operation of track switches, signals, and even automated scenery like crossing gates or lights. This multi-tasking capability ensures that all parts of the layout work together seamlessly, resulting in a fluid, lifelike railway operation.
In addition to controlling train motion, Mach 4 motion controllers can also manage feedback systems that monitor train positions, speed, and direction. This feedback allows the system to adjust train operations in real-time, avoiding collisions, ensuring smooth transitions between tracks, and optimizing the overall flow of the railway system. For example, when a train reaches a sensor placed on the track, the feedback system can signal the Mach 4 controller to slow down the train, change tracks, or trigger an event such as the opening of a crossing gate.
Integration with Other Systems
The true power of the Mach 4 motion controller lies in its ability to integrate with a wide range of other systems and components. This integration allows for the creation of highly sophisticated automated model railway setups, where various elements—ranging from train movements to scenery features—are all synchronized and controlled by the same system.
For instance, the Mach 4 motion controller can work in tandem with the USB I/O controller to monitor and control switches, sensors, and other trackside devices. The USB I/O controller serves as the interface between the computer and the physical components of the railway, while Mach 4 ensures that the motions and actions of those components are executed with precision.
The Mach 4 system can also be connected to slip ring systems, which are essential for providing continuous power and signals to rotating components. For example, turntables, cranes, and other rotating features require constant electrical connectivity to function properly. Slip rings ensure that power and data can be transmitted between stationary and rotating parts. By combining the slip ring system with Mach 4 motion controllers, hobbyists can achieve fluid, continuous motion for these elements without worrying about interruptions in power or signal transmission.
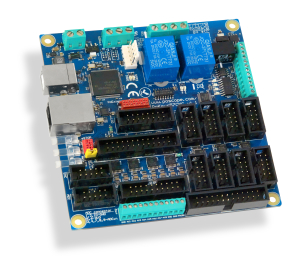
Additionally, the Mach 4 controller supports integration with other types of motion control devices, such as servo motors or pneumatic actuators. These devices can be used to control additional aspects of the model railway, such as controlling the height of bridges, the opening and closing of tunnel entrances, or even the operation of automated freight systems. The versatility of Mach 4 allows operators to extend their model railway automation to include complex mechanical systems, further enhancing the realism and functionality of the layout.
Creating Lifelike Scenarios with Mach 4
The Mach 4 motion controller allows hobbyists to create highly detailed and lifelike scenarios within their model railways. This is particularly evident when it comes to automating train operations. With Mach 4, operators can program realistic schedules for train arrivals, departures, and stops at stations, as well as the ability to handle freight operations, signaling, and emergency procedures.
For example, Mach 4 can be used to simulate realistic train movements such as gradual acceleration, deceleration, and even simulated delays. Trains can be programmed to make unscheduled stops at stations, switch tracks at junctions, and interact with signals and switches to avoid collisions or delays. The system can also simulate weather conditions, such as rain or snow, that affect train operations. These lifelike elements create an immersive experience that mirrors real-world rail systems.
In addition to train movements, Mach 4 can control automated scenery elements to add to the realism of the layout. For example, when a train approaches a certain area of the layout, the system can trigger events such as the opening of a gate, the activation of crossing lights, or the movement of a signal arm. Automated scenery can also include features like moving cranes that load or unload freight, or even scenic elements that change according to the time of day, creating a dynamic and evolving layout that feels alive.
Benefits of Using Mach 4 in Model Railway Automation
Using a Mach 4 motion controller in model railway automation offers several key benefits. First, it provides extremely precise control over train movements and other automated elements, ensuring smooth, lifelike operations that would be difficult to achieve manually. The ability to control multiple trains and moving parts simultaneously allows for the creation of complex layouts that operate autonomously, reducing the need for constant human supervision.
Second, Mach 4’s flexibility allows it to be adapted to a wide range of model railway layouts, from small tabletop setups to large, intricate systems. The controller can be easily expanded to accommodate additional tracks, trains, and moving components as the layout grows. This scalability makes Mach 4 an ideal choice for hobbyists who want to build increasingly sophisticated layouts over time.
Third, the integration of Mach 4 with other systems such as USB I/O controllers and slip rings enhances the overall functionality and realism of the layout. By ensuring that all components work together seamlessly, Mach 4 creates a cohesive, synchronized railway system where all elements are in constant communication, leading to smoother and more reliable operations.
Challenges and Considerations
While the Mach 4 motion controller offers numerous advantages, it also comes with certain challenges. One of the primary hurdles is the learning curve associated with programming and configuring the system. Mach 4 offers a high degree of customization, but this also means that hobbyists must be familiar with the software and understand how to program the system to suit their needs. For those who are new to model railway automation or motion control systems, there may be a significant amount of time and effort required to master the software and achieve the desired results.
Another consideration is the cost of the Mach 4 system, which, while offering great value for its capabilities, may be a significant investment for hobbyists with limited budgets. However, for serious model railway enthusiasts or those working on professional-grade layouts, the precision and versatility offered by Mach 4 often justify the expense.
The Mach 4 motion controller is a powerful and essential tool in the world of model railway automation. Its ability to control complex motion tasks with precision and flexibility allows hobbyists to create lifelike, dynamic railway systems that operate smoothly and autonomously. By integrating Mach 4 with other components such as USB I/O controllers and slip rings, model railway operators can achieve a level of realism and automation that was once reserved for large-scale, real-world rail systems. While it requires some investment of time and resources, the benefits of using Mach 4 are clear: unparalleled control, seamless integration, and an immersive experience that transforms any model railway layout into a highly functional and interactive miniature world.
Read also:
- Exploring Key Components in Modern Automation: CNC Pendants, 8 Channel Relay Modules, Automation Control Devices, and Programmable Relays
- Other articles from our partners
The Synergy of Automation in Modern Model Railways
In today’s world of model railroading, automation has transformed the way enthusiasts design and operate their layouts. By combining advanced components like the USB I/O controller, slip rings, and Mach 4 motion controllers, hobbyists are able to create dynamic, lifelike environments that operate seamlessly with minimal intervention. Each of these elements plays a crucial role in enhancing the realism, precision, and functionality of model railway systems, but it’s the integration of these technologies that truly sets modern model railways apart.
The USB I/O controller serves as the vital bridge between the software and the physical elements of a model railway, allowing for the precise control of switches, sensors, and signals. It is the backbone that supports automated operations, ensuring that every action, from track switching to lighting control, happens with synchronized efficiency. Coupled with the slip ring system, which ensures continuous electrical power and signal transmission for rotating or moving components, model railway operators can achieve smooth, uninterrupted motion. These components—though essential on their own—work most effectively when integrated together into a cohesive system.
At the heart of this automation is the Mach 4 motion controller, a highly versatile system that ensures the precision control of moving trains and automated scenery. Whether it’s coordinating the movement of multiple trains, triggering signal changes, or controlling mechanical elements like turntables or cranes, the Mach 4 motion controller allows operators to program, adjust, and fine-tune every aspect of their layout for maximum performance. It offers the precision needed to manage complex tasks simultaneously, ensuring that a model railway not only operates smoothly but with a level of realism that makes it feel alive.
By embracing these technologies, model railway enthusiasts can achieve a level of automation and realism that was once unimaginable. The ability to control every aspect of a layout—down to the finest details like weather conditions, train schedules, and moving scenery—creates an immersive experience that mimics real-world rail systems. This integration also offers significant practical benefits, including enhanced reliability, ease of operation, and the ability to scale up layouts without sacrificing control or functionality.
However, it is important to remember that while these technologies offer tremendous potential, they also come with learning curves and the need for ongoing maintenance. Mastering the use of tools like the Mach 4 motion controller and performing regular slip ring testing requires time, effort, and an understanding of both the software and the hardware involved. Yet, the rewards of achieving a fully automated, highly detailed, and smoothly functioning model railway are well worth the investment.
Ultimately, the future of model railroads lies in the continued integration of these advanced technologies, allowing hobbyists to push the boundaries of what’s possible and craft rail systems that are more complex, interactive, and enjoyable than ever before. The combination of USB I/O controllers, slip rings, and Mach 4 motion controllers ensures that model railway automation will continue to evolve, offering both novice and experienced enthusiasts the tools to build and operate incredible miniature worlds with precision, reliability, and creativity.